Milling Machines Tool-holding
- Customer Support
- Apr 2, 2021
- 5 min read
Updated: Aug 3, 2023
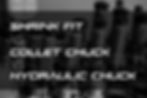
Everybody being it an owner, manager, programmer, or setter who is in-depth into CNC machining is familiar with the fact that the investment, the accuracy, reliability, and precision for a milling or mill turning machine operations is not complete with the sole purchase of the machine itself. Besides the fixtures and work holding devices and the tooling, a great investment and a major factor for the accuracy, ease of use, and reliability of the machining process is the tool holding choice. Today there are many special types of Milling Machines Tool-Holding and tooling solutions to suit best to the intended application. However, the scope of this comparison will be between a few general types which are most commonly used - the collet type, hydraulic, and shrink fit.
Being useful for separate qualities of their own and having their pros and cons, it is very often subject to making a Milling Machines Tool-Holding solution between one of them. However, when deciding which one to use it is their differences that will guide your choice. In order to make a liable comparison, we will try to look at the most important aspects of this decision-making by looking not only at the technical but the economical facts as well.
Precision & Security
We have to start with putting on the scale one of the most important factors. If you think a runout of 0.0005in could be acceptable you have to read this - studies show that run-outs of 0.00008in can triple the tool life, meaning that poor precision could be absolutely detrimental and lead to increased tooling costs.
Actually, the three types of tools can show very similar results as far as it concerns accuracy. With radial runouts less than 0.003mm or 0.00011in achievable with all types, it is out of the question that we can get the desired results. Even some ER types of collets which suffer from pullout stability and torque transmission, are able to deliver 0.002-0.005mm or 0.0001-0.0002in. However, there are other collet type holders like the so-called power chucks being far more superior in terms of power. They have features like axial slits to prevent tool rotation and radial ones preventing the tool pull out. The gripping force of these chucks is powerful enough to actually compress the tool shank slightly and expand into the slits. Tests show that the chucking torque force can deliver up to 5000Nm or 3700lbf and this combined with an acceptable radial runout of less than 0.00019in.
Shrink fit and hydraulic tool holders are offering unsurpassed gripping and high clamping torque and no centrifugal forces due to clamping segments. Depending on the clamping diameter the hydraulic ones can deliver over 6500nm (4795lbf).
The hydraulic tool holders offer higher holding forces of shrinking, high torque transmission, and bending distance 1.4 times greater than shrink chuck. A big plus is the dampening effect due to the cushioning of the hydraulic membrane. The shrink system on the other side is a bit less reliant in terms of vibration because of its dependence on the heating and cooling processes.
Variativity & Flexibility
When talking about making choices it is of great importance to know the limits and restrictions of the different tool holder types. Generally speaking, the collet chucks are the most versatile ones as they can come in different standards and sizes, different sized collets, and even size ranges for them. They can conduct coolant in a different way just by switching to a different type of collet. As well as with the hydraulic ones that have sleeves they can both use a through coolant channel system for tools without coolant holes to deliver it directly to the cutting edge. On the other side the shrink fit can only use flush or through coolant which makes it a bit more demanding for delivering it well for milling operations.
While considering the accessibility, the collet type chucks cannot offer as good as the shrink fit and the hydraulic solution. The collet chuck is comprised of a collet, holder body, and a cap which is comparatively much bigger than the maximum size of the tool to be clamped. Although an extension can be employed it will compromise both the gripping force and the accuracy.
Actually, the shrink fit tool holders were unsurpassed in terms of accessibility because of their elongated design, a fact which with the advance of 3D metal printing technology changed to a great extent. Now on the market, you have hydraulic systems allowing for deep reach and side clearance comparable to the shrink fit systems.
It must be noted that an important feature to look at while choosing the hydraulic is the position of the membrane as not all tool manufacturers would offer to have it from the front of the holder meaning that for smaller applications the tool will be supported further from the cutting zone. Also, the clamping depth has a minimum before which it is not recommended to use.
Setup & Maintenance
Probably you can guess that the shrink fit is most uncomfortable because of the heating and cooling processes involved. An inconvenience for an operator will not only be the risk of burning but the wait for the cooling before the tool can be used. Hydraulic systems can lock the tool simply by tightening with a hex wrench or a sector key which is the most common case with the collet types too.
Initial Investment
As we already discussed some of the pros and cons technically we should now look at the numbers behind the investment. Being the newest and more advanced technology the hydraulic tool holders have relatively highest prices among all. This is because of the delicate clamping membrane built into the holders which adds cost.
Besides the smaller sized ones that can only clamp a single diameter the reduction sleeves available are about $150 at least. The same is the situation with the power chucks from the collet type holders and only the ER type collets and the ER holder itself or similar could be of low price
Shrink fit holders are of a slightly lower price than the hydraulic chucks. However, the major difference for this type of solution will be the induction heater shrink fit machine which starts at prices around $4000.
Conclusion
Having exposed all the above it is clear that each and every solution has its advantages over the other two. Being based on the accuracy, price, accessibility, or whatever factor it will be difficult to stick to only one of the tool holder types. Therefore order to get the advantage of the features of the three tool types to offer most. Shops wouldn't use only a single type, but a combination, if not all of them. Which ones you will choose is up to you!